Our Process
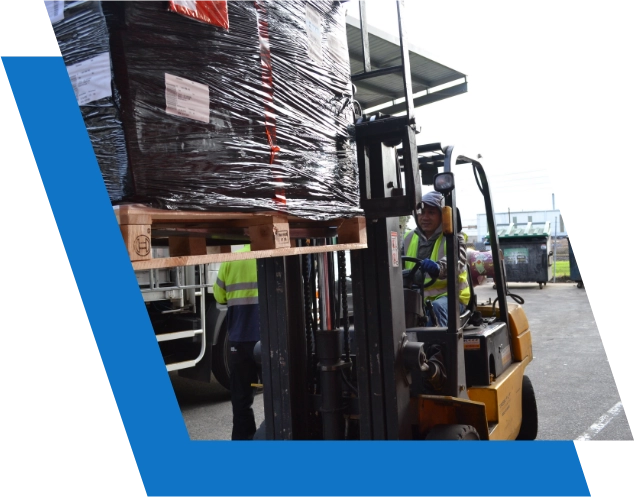
Custom logistics, backed by superior quality
At Bettapak, we don’t just meet standards – we set them. Our commitment to excellence is woven into every aspect of our operations, ensuring that all work is completed in accordance with your individual requirements and relevant statutory provisions. This precision is achieved through our robust quality management systems, which guide the planning, execution, and inspection of every task affecting the standard of the finished product.
From the first touchpoint to the final delivery, your custom logistics are in expert hands, allowing you to trust in the quality and compliance of every package we handle.
What to expect
1. Establishing SLAs / agreed order volumes per day
Together, we will establish mutually agreed packing guideline standards and minimum order amounts per day. This sets a precedent for the level of service you can expect and allows you to plan around deliveries and order volumes. When spikes hit due to seasonality or sale periods, we will have regular meetings with you to ensure the uplift is catered for.
2. Quality control
2. Quality management logistics We’ll work with you to establish robust Quality Control (QC) checks tailored to your specific job requirements. This ensures our standards align perfectly with your expectations from the outset. Once production begins, our team leaders will conduct regular inspections and spot checks based on these controls. This maintains consistency and catches any potential issues before they arise, giving you the confidence that your product is receiving the utmost care and attention at every stage.
3. Final inspection
As we prepare for dispatch, we’ll open one box from every pallet to conduct a thorough inspection. This isn’t just a cursory glance - we meticulously compare each item against the Perfect Sample we established at the project’s outset. In the unlikely event that we spot any product faults or variances, these items are immediately isolated from the rest, and the affected stock is swiftly moved to a quarantine area. This exacting process ensures that the products leaving our facility are nothing short of the standard we promised.
4. Dispatch
During the dispatching process, we palletise your goods exactly as we’ve mutually agreed, following any specific instructions to the letter. Each pallet is then cocooned in protective stretch wrap and equipped with a comprehensive identification tag, containing all the crucial information needed for smooth logistics operations. Every dispatch load is also accompanied by its own unique delivery docket, and you are provided with all relevant dispatch details.
5. Reporting
You’ll be provided with regular reports to give you a clear window into your project’s progress, offering optimal supply chain visibility. These reports include up-to-date information on job tracking, accurate counts of completed units, breakages or faulty goods, and any challenges or issues that may arise during production, along with our strategies to address them.
Questions or concerns?
Get a quote today
Ready to take advantage of quality logistics solutions?
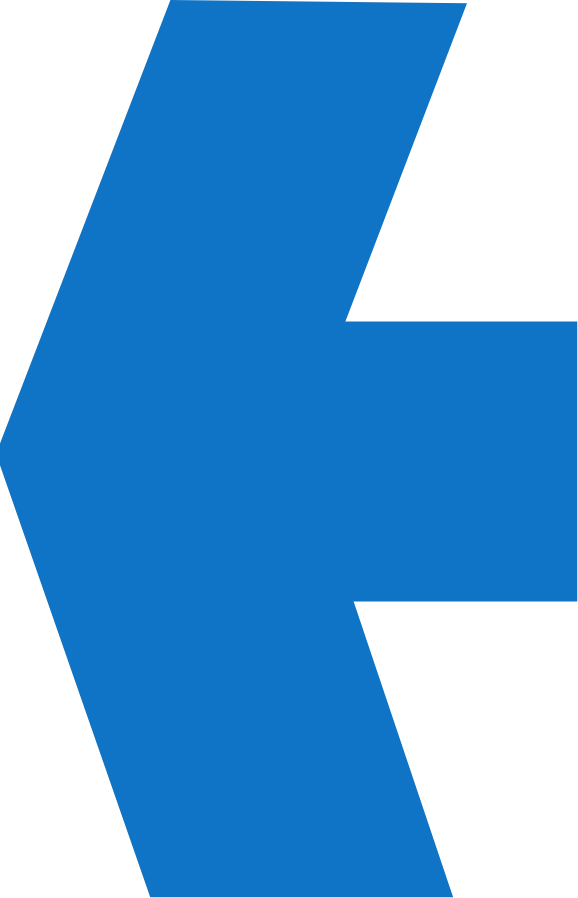